Both consumers and manufacturers are very concerned about food safety. Despite our desire to believe that our food is uncontaminated, trace metals and particles can pollute it. In processing facilities that use large machinery and handling equipment to sort, package, and convey goods, these undesired particles mingle with our meals.
These devices may leak metal pollutants into the food products they handle because to wear and tear from continuous usage. When “extraneous metal elements” were found in nearly 50,000 pounds of beef in 2015 alone, Unibright Foods had to recall it. Such events are regrettable, but they serve as a useful reminder of how important it might be to utilize food safety metal detectors on production lines.
The food safety of their products is ensured and manufacturers can stop contaminated food from reaching customers. The first two stages to raising food safety quality at your plant are knowing what metals to look for and how to detect them.
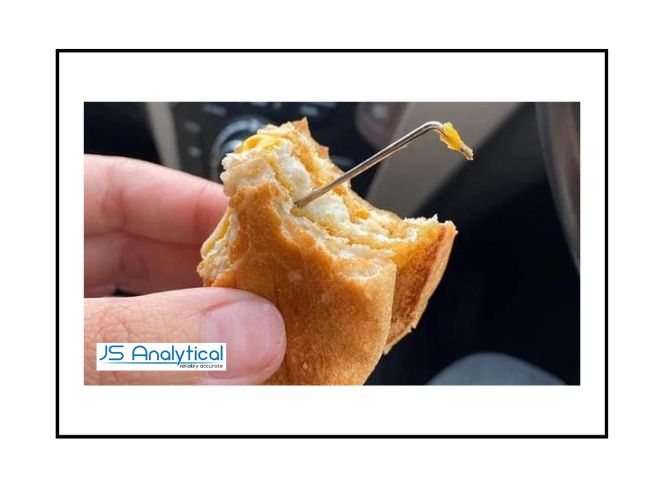
Common Contaminants Detected by A Food Safety Metal Detector
These gadgets can now identify even the tiniest amounts of metal thanks to advancements in metal detection technology. The magnetic permeability or conductivity of metal particles is detected by the food safety metal detectors themselves. They primarily identify three categories of metal types:
- Ferrous Metals (Mild Steel/Cast Iron) – Ferrous metals contain iron, an element with strong magnetic properties. Their magnetic properties make these metals especially easy to identify with food safety metal detectors, which pick up on the magnetic field emitted by trace amounts of iron.
- Non-Ferrous Metals (Copper/Lead/Aluminum) – These metals lack iron and are not magnetic. However, they are still conductive. The electromagnetic resonances in these metals make them fairly easy to detect.
- Stainless Steel – Although stainless steel does contain iron, it does not possess strong magnetic properties. It is also less conductive than the other elements on this list, making it more challenging to detect. Environmental conditions such as moisture and high salinity can also interfere with detection.
Knowing what kinds of food safety metal detectors are available and how to use them efficiently in your production facility are equally important as understanding why metal detection is essential in food processing. Depending on the types of foods you manufacture, the systems processing those foods, and the space available in your facility, you’ll need a certain type of food safety metal detector. Each kind examines food items with various characteristics.
Food safety Metal detectors for conveyors – As the name suggests, you can find these detectors next to belts that transport food safely between machines or workstations. Each item on the belt line is examined by these gadgets that hang overhead as it passes beneath the electromagnetic field of the detector.
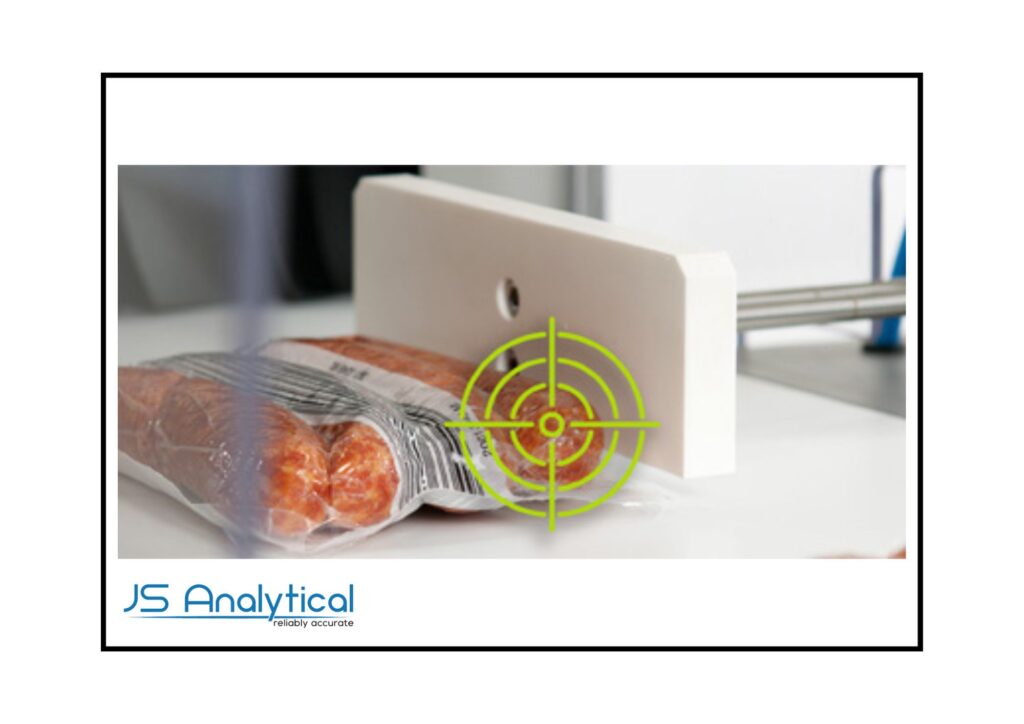
Reasons A Food Safety Metal Detector Is Essential for Food Industry
- Metal detection is the sole method available for detecting metal microparticles released by the deterioration of your processing equipment. A food safety metal detector is vitally necessary to ensure that there is no chance of metal impurities causing customers to become ill. Other methods, such as quality assurance checks by eye, can’t pick up these tiny pieces of debris.
- In connection with this, high levels of micro metal contamination in your food safety processing activities are another sign that your manufacturing equipment might malfunction. This can assist you in setting up preventative maintenance for your device before it malfunctions in the middle of the job, costing you thousands in lost productivity.
- Metal detection also helps you save a ton of time throughout the quality-control procedure. It is less necessary to perform time-consuming manual quality checks when using metal detection equipment that is low maintenance and can be configured automatically. Instead, worker time would be better spent on management solutions.
Finding the tools, you need to start your assignment seems like a logical next step after learning how food safety metal detectors aid to increase food quality and food safety. It’s crucial to remember nevertheless that not all equipment is created equal.
Factors That Can Affect Food Safety Metal Detection Results
In the past, meals high in minerals, such as leafy greens, salty meats, and cheeses, may trigger a metal detector because of their inherent mineral content. Similar factors like the temperature of a food safety processing facility and the air’s salinity can frequently affect the outcomes. The electromagnetic fields of large machinery close to the detector have the same properties.
Because of recent improvements in metal detection technology, these interference problems can now be avoided, allowing operators to tune out irrelevant signals and concentrate on particular components and frequencies. Food safety processing facilities can now identify extremely small amounts of metal in food thanks to smart detecting technology that scans frequencies.
Always verify your food packaging for the presence of aluminium foil or other metals before utilizing a food safety metal detector at the end of a production line. The packing material can still trigger your device even though it is not in the meal itself, leading to false positives. Request a product test from one of the manufacturer’s certified inspectors to confirm the proper installation of a food safety metal detector in your establishment. The inspector can evaluate the device’s functionality in your factory and adjust it for that setting.
Pros Of Food Safety Metal Detectors
New technology offers maximum sensitivity for contaminants
Modern sophisticated metal detecting devices are built to give the highest level of sensitivity for pollutants. They also maintain a high resistance to interference, which is crucial.
You can train the food safety metal detector for specific products
Less manual adjustment is therefore required for various items. The production increases, anticipated downtime decreases, and changeovers become quick and simple.
Food safety Metal detectors can be installed almost anywhere along your line
Your system should ideally be installed at the point in your processing line where impurities are most likely to be found. Food safety Metal detectors have an advantage in this situation since they may be positioned practically anywhere along the line.
X-ray inspection systems for unpackaged products
Our food safety metal detector X-ray scanners are specifically built for the food industry and give excellent performance for the inspection of unpackaged bulk items while adhering to all vital food industry requirements.
The bulk material is uniformly distributed throughout the whole width of the conveyor belt and examined with extremely high detection accuracy via an integrated feed hopper with an optional vibrating chute. Our RAYCON D+ BULK Series sensors detect not only metals, but also pollutants such as glass, pottery, stones, raw bones, PVC, and so on. As a consequence, they combine extremely efficient pollutant detection with maximum simplicity of use and a sanitary design.
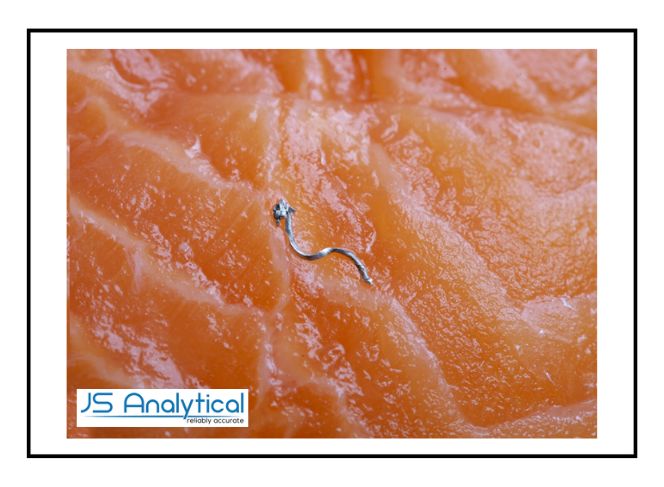
Comprehensive product inspection with X-ray systems for food safety metal detector
The food sector prioritizes product quality above everything else. Manufacturers are responsible for the contamination, and contaminants and quality flaws can damage a company’s reputation. Our X-ray inspection systems for food safety, identify a wide range of pollutants and product faults, protecting you from customer complaints and product recalls while protecting customers from health risks.
Any pollutants whose density differs considerably from that of the product being inspected, as well as air bubbles, fractures, and other faults, are detected by food safety X-ray inspection equipment. Our food-inspection X-ray systems for food safety use a conveyor belt to pass your items uniformly through the X-ray beam.
The radiation is converted into an electrical signal by the detector mounted above the conveyor belt. Our specialized analysis software generates a digital X-ray image from this, which inspects for impurities and product faults. Integrated separation systems guarantee that impure or faulty goods are reliably removed.